How to Avoid L.A.’s Rapidly Increasing Warehouse Rent Costs
If your business requires warehousing and distribution, you’re probably aware of the increasing costs of warehouse rent – especially on the west coast, and specifically in Los Angeles. In fact, warehousing rent costs have increased by 300+% in the last year alone. This rate is alarming and hindering distribution businesses and their customers, so why is it happening? Learn more from one of our experts below, followed by our tips for avoiding this costly scenario for your business.
With high volumes of traffic and congestion (homes, people, and businesses), and a lack of zoned land for warehouse space, it’s becoming increasingly difficult for warehousing and fulfillment centers to operate in L.A. Other contributing factors are the overall increase in labor costs, lack of experience with individuals newly entering the workforce, and the rapidly growing demand for warehousing space in a booming city. Warehousing professionals generally consider a 4-5% vacancy rate as a normal healthy market, whereas LA has been sitting below 1% for three consecutive years. This is an unprecedented confluence of events. Previously, 25-40% warehouse rent cost increases were the high norm, and now the numbers we’re seeing are unheard of. This makes it difficult to grow and presents a number of other challenges.
How Did We Get Here?
For many years, L.A. has been a growing market due to the reasons we stated above. With growth in e-commerce and a continued, strong import stream from Asia, it’s the largest port on the west coast. But when COVID-19 hit, there was an increased demand for retailers to buy products that weren’t moving, and therefore, the need for more storage solutions.
How Long Will Warehouse Rent Increases Last in Los Angeles?
In theory, volume increases seem like a good thing because it means demand for goods is high. People want to buy. On the flip side, this increased demand creates the need to store more inventory, and in major real estate markets like Southern California and Southern New Jersey, space has become costly and supply has been consistently outpaced by demand.
The good news is that now that we’re moving further away from COVID, supply chains are beginning to streamline again and industry levels across the board are rightsizing.
How Can Companies Respond and Avoid These Rising Warehouse Costs in L.A.?
Unfortunately, there are limited options for avoiding high rent costs, especially if a business is trying to remain in L.A. Trying to squeeze out additional space by updating racking, or reconfiguring existing space is one option, but that’s not always feasible. Our best recommendation at the moment is to try and relocate your warehouse elsewhere. For example, Sacramento has proven to be a more cost-effective solution.
If you’re able to move locations in California, you’ll discover more competitive drayage rates and labor markets with the ability to grow within that location. You’ll have more staff and space to choose from, with more flexibility to boot. Before making the move, an expert 3PL like G&B Fulfillment, can help you assess your outbound service levels, test effectiveness of B2B and parcel methods and more. With a new location, you’ll find your business with more money that can be invested into making the business more successful.
Why G&B Fulfillment Chose to Open Warehousing Facilities in Sacramento
Business growth comes with great success, and at G&B Fulfillment we were fighting to get into the hotter markets to keep up with client demand. With increasing costs across the market, we did not believe we could effectively meet the needs of our fulfillment customers while staying in L.A. We started considering other nearby options that provided us:
- available warehouse space and labor
- access to Asian imports via nearby port
- easy transportation to the rest of our country by truck or rail
We’ve really come to understand why location matters for 3PLs. Many companies think California, as a whole, is difficult to break into the market, but when you’re able to get into a building of a similar size in a less congested market, rent, labor and inventory costs settle. Sacramento also allows direct port transactions from Asia at similar rates previous to the boom.
If you’re seeking breathing room in all aspects of your growing distribution business, consider relocating to a city that still has strong railways and highways and is enough of a major hub to keep your supply chain operating smoothly.
Talk to our experts at G&B Fulfillment and we’ll help you combat the ridiculously high warehouse rent costs in Los Angeles. You’ll be glad you left behind the expenses and inefficiencies for a more successful solution.
Talk to an Expert
You May Also Like
These Related Stories
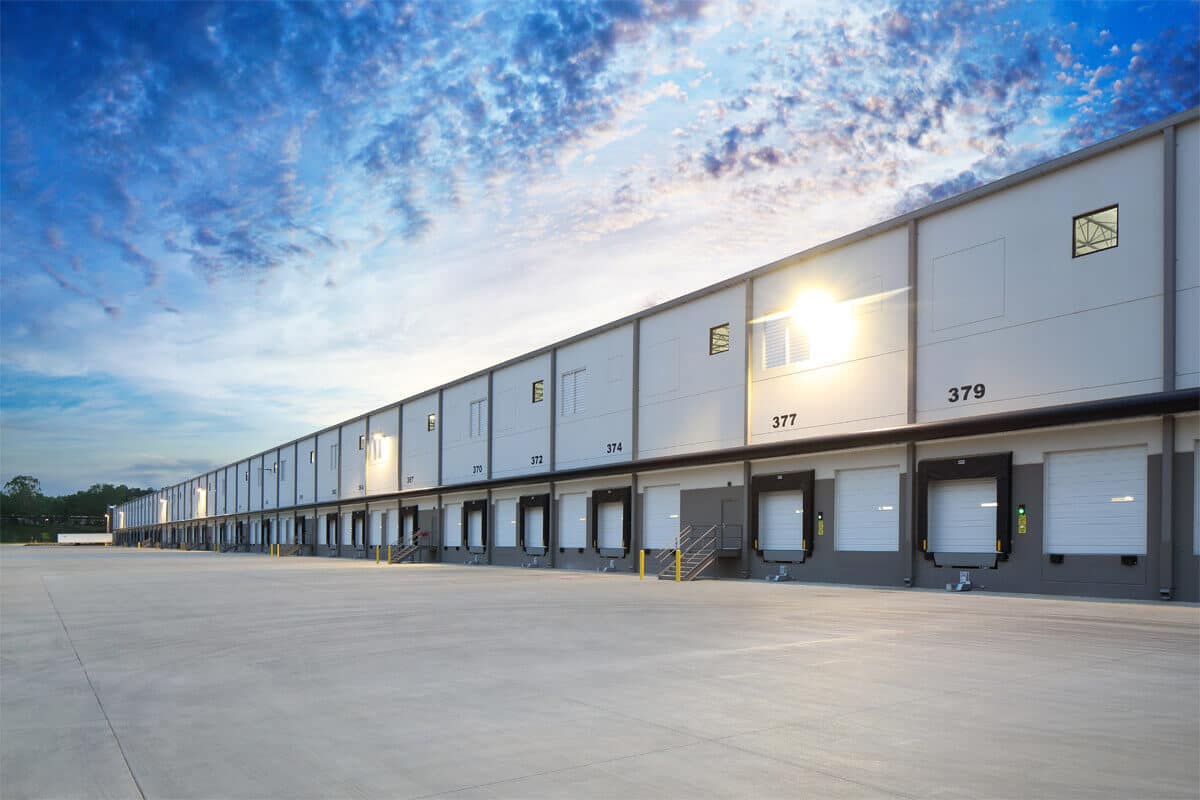
Exploring Sacramento’s Premier 3PL Warehousing Solutions
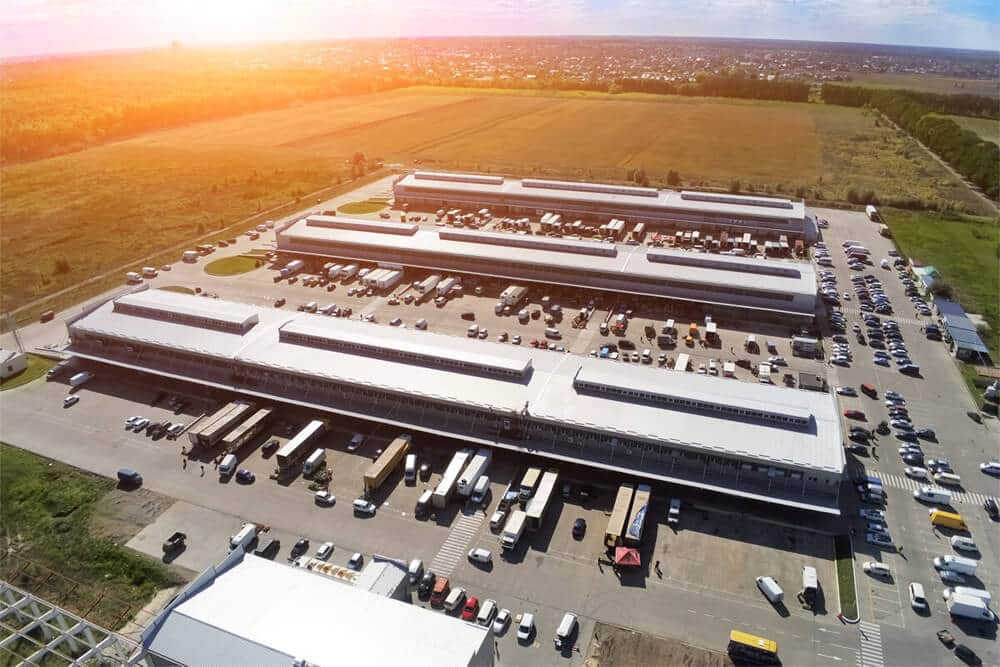
The Advantages of Choosing a 3PL Warehouse in a Strategic Location for Your Business
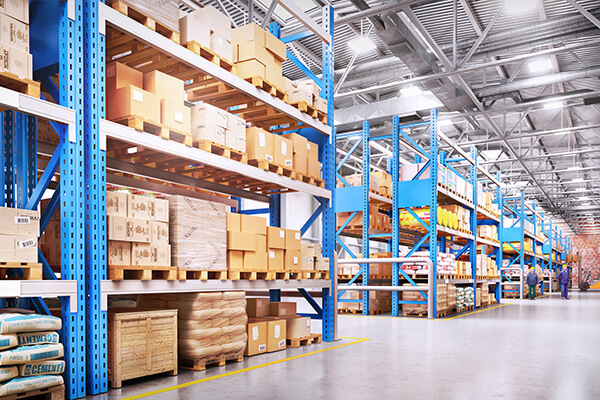