Why You Should Ask About Your 3PL’s Warehouse Safety Practices
Warehouse safety is a significant concern, with the warehousing industry ranking near the top in injuries annually, according to the Bureau of Labor Statistics. When choosing a third-party logistics (3PL) partner, it’s important to work with a company that has safety at the forefront of its operations.
The biggest reason, of course, is the people. No one wants to work with a company that doesn’t take care of its employees and prioritize their health and safety.
Safety Is Good for Business
Beyond the human factor, safety helps your business run more smoothly and predictably. If you're working with a partner that doesn't have proper safety protocols implemented, you could be rolling the dice.
Warehouse safety is instrumental for smooth 3PL operations and providing the best service to clients.
Having strong safety protocols in place and processes to reinforce them can:
- Reduce cost (for the 3PL company as well as their clients)
- Reduce risks
- Lower employee absenteeism and turnover
- Increase productivity and quality
- Raise employee morale
- Lessen the threat of legal action
- Keep operations running smoothly
On the other hand, not focusing on warehouse safety can be detrimental. More accidents are likely, and that leads to fewer workers available for shifts and slower service levels. Not having control of safety practices can also indicate that the company doesn't have control of its entire operation.
Partnering with a 3PL provider that doesn’t take safety seriously can affect your timelines, costs and quality. If a 3PL employee gets hurt, the company not only needs to stop and help investigate what happened, but it also needs to pull people off other tasks to take over the person’s responsibilities. There can be equipment involved in the accident that may need to be pulled off the line as well. Overall, it’s a snowball effect that significantly slows down the day-to-day operations, which, in turn, slows down yours.
The concept of employee morale is especially important. An employee that feels unsafe isn’t going to want to put in their best work. If they or a coworker is injured on the job, it can impact their confidence, lower their motivation and possibly cause them to seek employment elsewhere. An engaged employee puts in their best effort, meaning the quality of their work is higher (which translates to better service for you).
To feel at ease with your selected 3PL provider, start with some basic questions to understand their approach to warehouse safety. Consider the following:
- What processes do you have in place to reinforce safety?
- What is your protocol when an accident occurs?
- What can I expect if an accident impacts my timeline or product quality?
- How does your team train for high-incident tasks?
- How do you communicate with your clients about accidents?
Committing to Warehouse Safety
At G&B Fulfillment, we take our employees’ safety very seriously. Our processes address a variety of aspects that impact safety in the warehouse, making sure that workers are confident and careful.
Here are some of the measures we take:
- We keep all workspaces clean and organized is a top priority: Doing so helps limit the risk of tripping and falling and ensures the environment allows for efficient work.
- We only allow certified personnel to operate equipment: This ensures proper equipment operation that doesn't result in safety incidents.
- We define forklift paths to optimize safety and efficiency: This way, forklifts aren’t crossing into zones more likely to cause accidents.
- We supply and wear personal protective equipment (PPE): This includes hardhats, goggles and gloves to protect our workers.
- We inspect equipment daily to look for defects, foreign objects, or anything that may increase the risk of accident or injury: This also helps keep our equipment running efficiently and reduces downtime for maintenance.
Our employees also take part in regular safety training, during which we review our safety plans and conduct practice drills. As a company located in California, we must keep natural disasters top of mind. We have developed emergency preparedness procedures for fire, lockdowns and natural disasters such as earthquakes. This helps our employees respond to real-life scenarios with efficiency and without panicking. Everyone knows where to go, what to do and where to exit.
Communication is absolutely vital to safety. We encourage communication across all departments and among all employees, at every level. This includes an open-door policy among management and the opportunity for anonymous feedback and suggestions. We hold (at least) weekly meetings with every employee to discuss the work ahead, celebrate successes and address concerns.
Let’s Talk
Partnering with a 3PL provider that keeps safety as a top priority is going to be best for you in the long run. Reach out to G&B Fulfillment today to learn more about our fulfillment services and safety practices.
Talk to an Expert
You May Also Like
These Related Stories
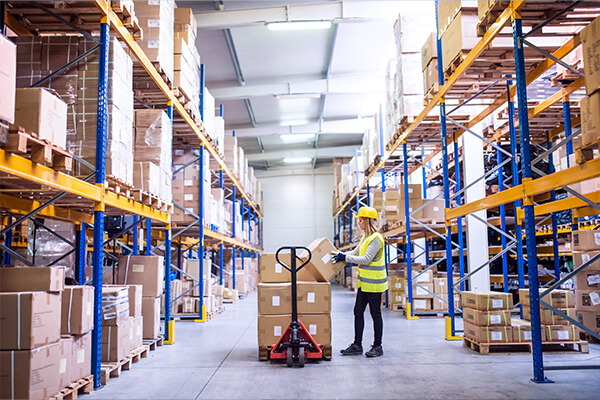
How Outsourcing to the Right 3PL Partner Can Help You Overcome Supply Chain Disruptions
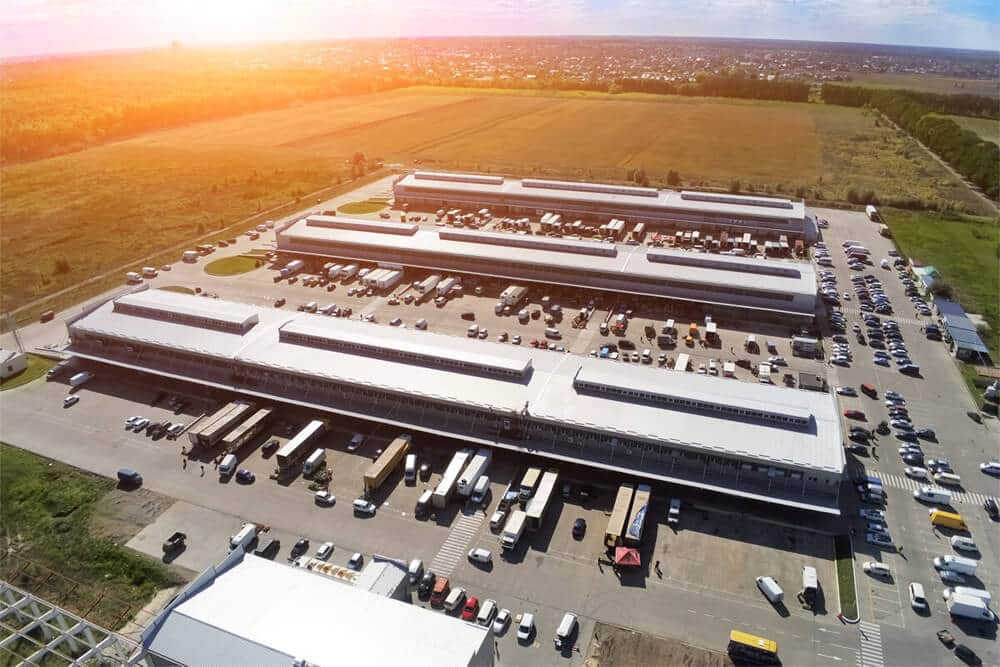
The Advantages of Choosing a 3PL Warehouse in a Strategic Location for Your Business
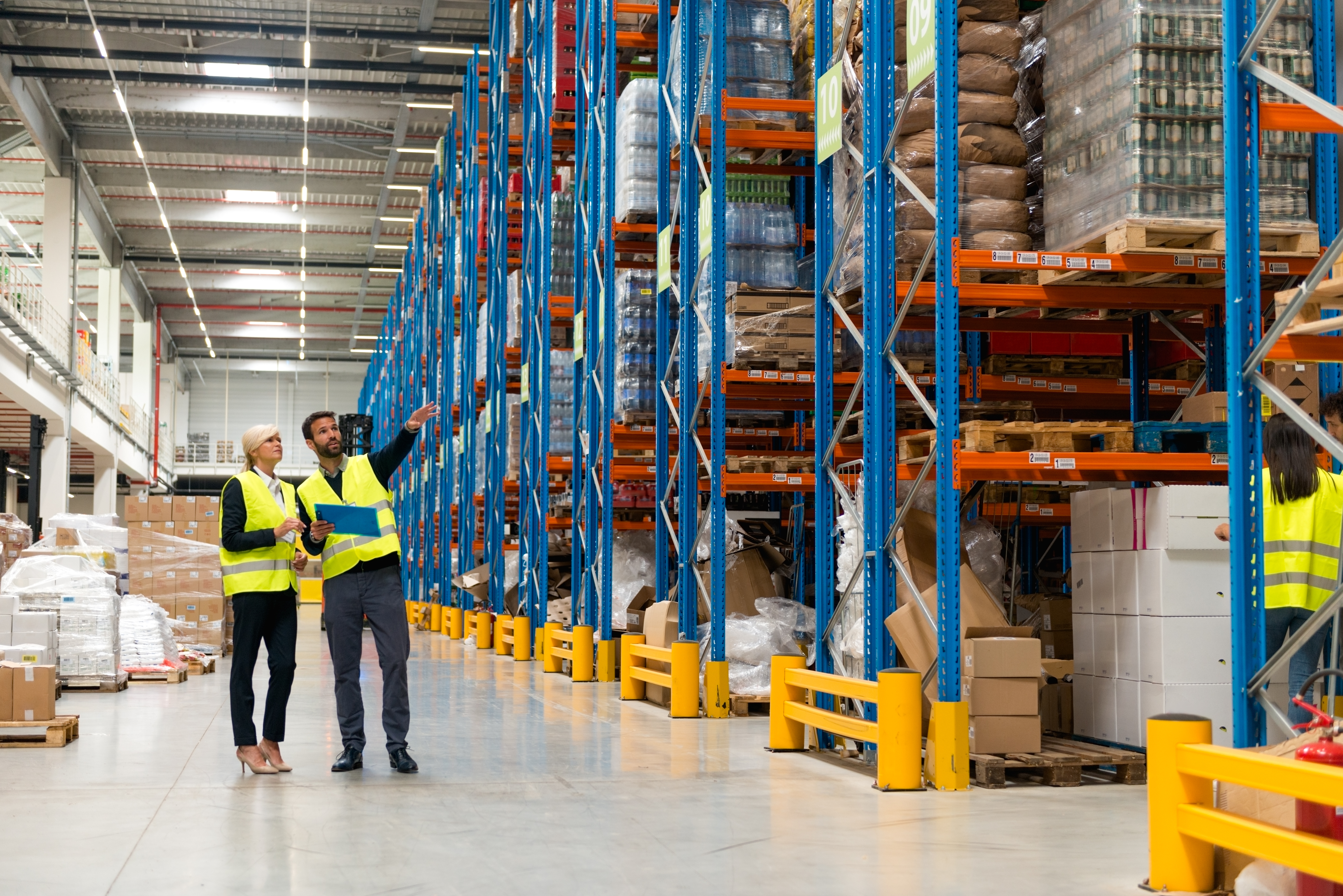