Solving Warehouse Labor and Safety Issues with Autonomous Mobile Robots: A Conversation with Matt Kelly
Faced with a declining pool of warehouse workers and a rapidly expanding ecommerce business, third-party logistics providers (3PLs) are relying more on autonomous mobile robots (AMRs) to fulfill challenging distribution and fulfillment contracts.
AMRs are similar to automated guided vehicles (AGVs) in that they employ sensor technology to deliver inventory around the warehouse. AMRs can navigate their environment through the use of computers, onboard sensors and maps.
This transition to robotic automation represents a significant paradigm shift for an industry that has traditionally relied heavily on manual labor.
If you’re like me, you may be considering introducing AMRs into your warehouse operations, but you need some answers first.
- How much is it going to cost?
- Is it really going to work?
- Is it going to provide a return on investment?
- Is it going to be flexible, like people, when things change?
I had the opportunity to speak with Matt Kelly, Account Manager at inVia Robotics, to get the scoop on autonomous robots.
The interview below has been edited slightly for clarity.
_____________________________________________________________________________________
Q: What types of autonomous robots are available?
Matt Kelly: Robotics is a big term, and it’s been around for a long time. What’s unique is that the robots that have been built in the last 5-7 years are autonomous mobile robotics. Their mobility makes them much more flexible. They can be used in greenfield and brownfield deployments, and then can be moved any time. That’s increased the adoption rate of robots in warehouses, especially those operated by 3PLs (third-party logistics providers).
The AGVs (automated guided vehicles)—ones that require tracks and a lot of infrastructure—are still popular, but those have a very different customer. They require a lot of investment, a lot of capital and a lot of foresight into where that organization is headed. You really need to think 10 years out on your ROI. I see the biggest interest in the 3PL market. They want flexible solutions like AMRs because the 3PL space is very unique.
Coming out of a pandemic, it’s never been more relevant. Why didn’t you find toilet paper at your grocery store? This is a question that comes back to the inefficiencies of logistics and supply chains. It is in that problem and that challenge that AMR technology, both artificial intelligence software as well as robotic platforms, are more relevant than ever.
Q: For someone who is auditing AMRs for their warehouse operations, what questions can they be asking themselves to help in the decision-making process?
A: For a lot of these companies, especially during Covid, the labor turnover rate has gone up significantly. With that, there is a tremendous amount of soft costs that have to be looked at and evaluated, not just how much you were spending on labor.
- How much did you spend to hire new people and train them?
- Can you automate some of those processes that are less technical and require less experienced labor?
- Can you redeploy that labor to other parts of the operation and let the robots handle goods-to-person picking and some of the other material handling tasks
Q: What industries are likely to use AMRs in their operations?
A: These robots would be specifically used for warehousing and the fulfillment of orders. That’s where the big opportunity for robotics and software really lies—in the storage and retrieval of goods—those touches that get the package to your door for an ecommerce-type of an order.
They are especially designed to make ecommerce order fulfillment faster and more efficient. Moving those orders through a warehouse is much more complicated than refilling stock in retail stores. It requires retrieving onesies and twosies instead of whole pallets of inventory. Creating a retrieval process for all of those individual, disparate items means you need intelligence from software that batches orders, and you need robots that can travel across the entire warehouse.
Q: What are some of the benefits companies can see by using AMRs in their warehouse?
A: Reduced labor costs and improved efficiency and accuracy are the big ones. Especially with Covid, you started to see labor being dangerous for the first time because you can’t have a lot of people close to each other and also have social distancing measures in place. So, if you can have the robots handling some of those picking tasks, you can also have a safer environment for labor to continue working and providing the value that only labor can.
Q: How do autonomous mobile robots navigate through warehouses? Do they offer 24/7 support?
A: For robots that are truly autonomous and work without being tethered to people, they are often working 24/7. So, you’ll want 24/7 support as part of your service contract.
There are two different approaches to mapping. Some companies have a mapping robot that will go around and map out the whole facility. Others, like ours, will map out the facility ahead of time, and then we’ll use that map in our simulation to direct the robots through a WiFi signal, essentially like GPS in the warehouse.
Most robots in this space will be able to pick up issues (you don’t want them running into people), so they’ll be able to determine where there’s an obstacle that they have to adapt to. That’s why they’re autonomous, mobile and flexible.
Q: What’s the difference between AMRs and AGVs?
A: AGVs move items back and forth from point A to point B all day long, and they’re usually controlled by a robotic operating system or via tracks in the warehouse. AMRs are flexible systems that can move based on the orders and artificial intelligence, and they can go anywhere commensurate with the needs of the operation. So, when an order drops, the robot goes to the right location at the right time. Whether it’s picking, replenishment, whatever the task, it’s the system that’s going to direct it. It’s not the track or an operator controlling the robot.
That’s where the real efficiency is; not having a manager or an admin sit there and map out how the robot moves throughout the facility. At inVia we provide a system that can eliminate 100% of the distance a worker travels. The average warehouse worker walks about 12-15 miles a day. Any robotics system that can eliminate people traveling that distance is definitely one that people should look at. If you want to reduce your labor by 50 to 70%, you have to take out the travel factor.
Q: Why would someone be hesitant to incorporate robots into their warehouse operations?
A: A lot of companies see this as a massive investment, and they lack the experience to feel comfortable making that investment. What we have found beneficial is to start with a flow management software layer that provides intelligence. Business leaders want to make the right decision so that they grow profitably and they grow sustainably. Our system provides the intelligence to know how many robots you need and how many people you need for that day.
Automating and dropping in AMRs once your operation has become more efficient with AI software is actually very easy. These are flexible systems and we flex it at peak. We’ll send 40 extra robots to a site to handle peaks; that’s easy to do when the customer has the intelligence to know they need that, and that’s so critical. I can’t stress enough how important it is to have that level of intelligence and visibility into how things are operating. Without it, you’re making decisions blindly and prone to making bad decisions.
Should You Consider Using Autonomous Robots in Your Facility?
With the increase in technology and competition in warehouses, using autonomous robots in your facility should be considered. Every warehouse can benefit from robotics. Not only do they have the ability to improve operations, but they also increase material handling productivity, accuracy and customer satisfaction.
As you decide what’s best for your operations, ask yourself the following:
- Where are your current warehouse bottlenecks?
- Do your workers spend a lot of time retrieving goods?
- Do you spend too much time taking inventory counts?
- Do you find yourself running out of goods due to inaccurate inventory?
If you’re interested in learning more or need help in your robotics journey, contact us today to start a conversation.
Talk to an Expert
You May Also Like
These Related Stories
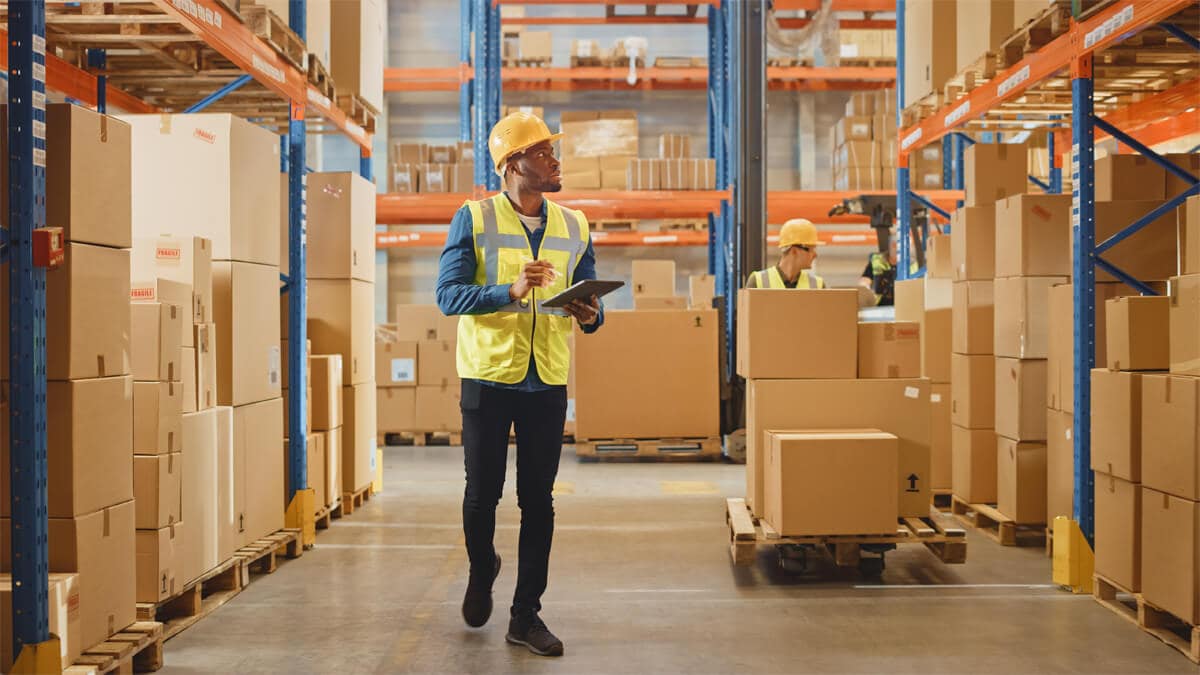
Fulfilling Your Own Orders vs. Working With a 3PL
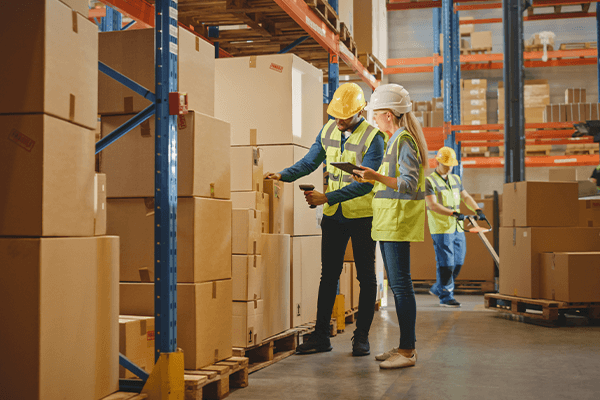
Why You Should Ask About Your 3PL’s Warehouse Safety Practices
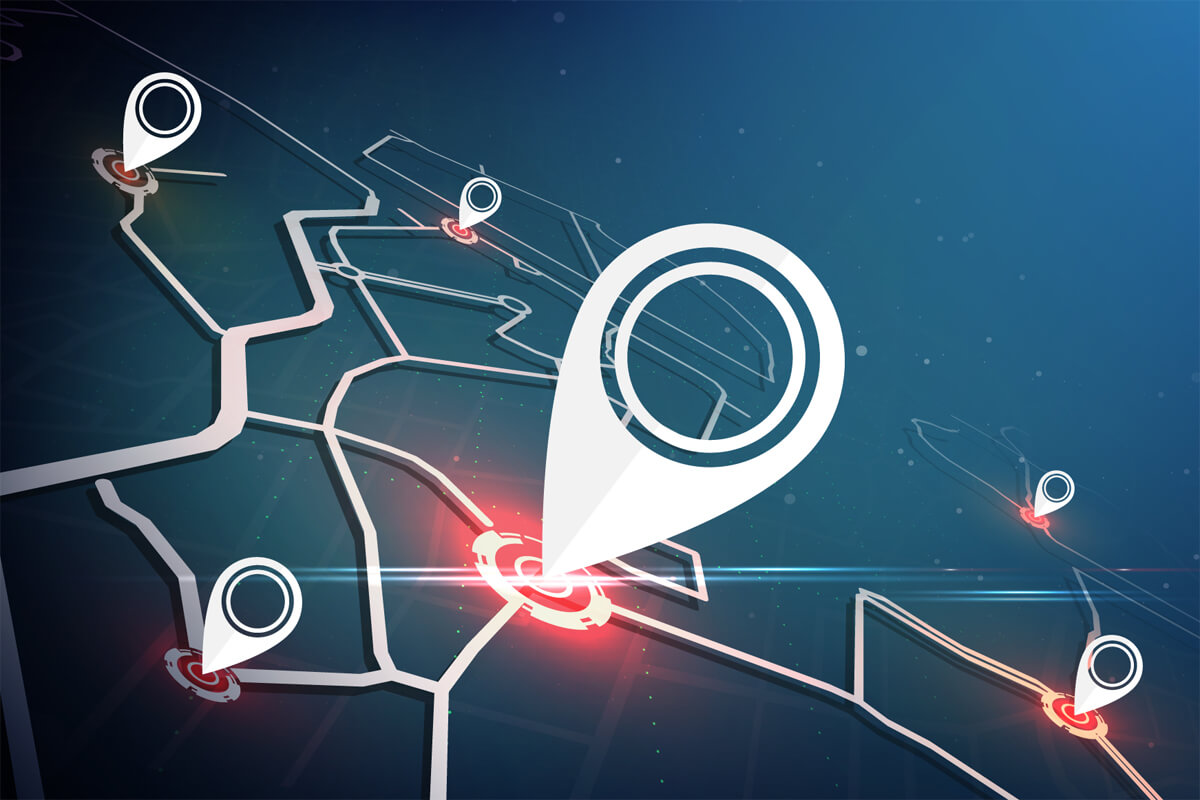